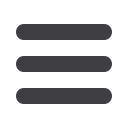
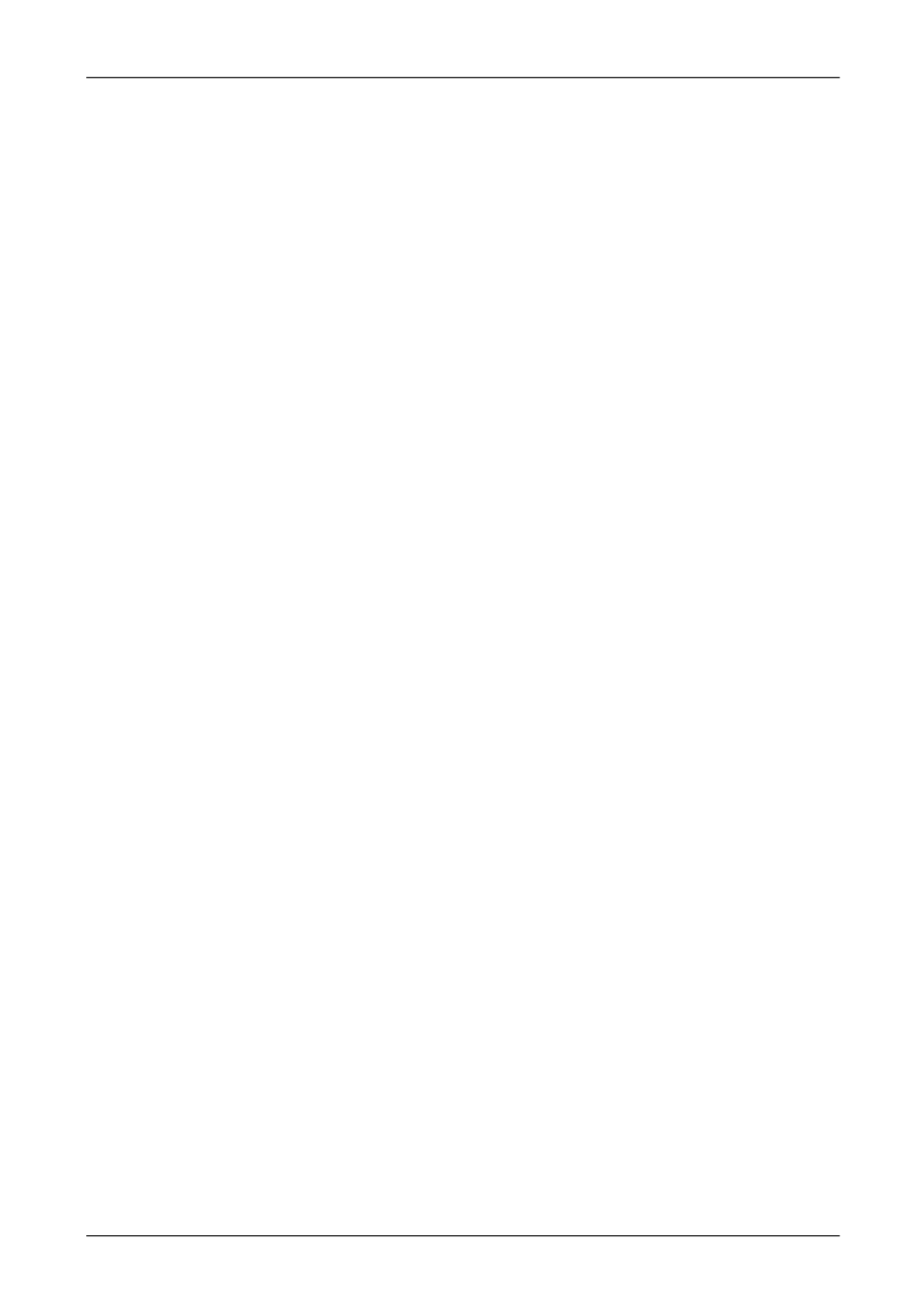
Механики XXI веку. №16 2017 г.
94
Введение.
В настоящее время для изготовления деталей все чаще применяются мате-
риалы, обладающие высокими прочностными свойствами, что обусловлено развитием тех-
нологий и необходимостью совершенствования узлов и механизмов различных устройств.
Традиционные конструкционные материалы, такие как стали и их сплавы, цветные металлы
и их сплавы, способны обеспечить требуемую прочность деталей, однако имеют высокую
стоимость и значительную массу. Для устранения этих проблем в промышленности реали-
зуются технологии изготовления деталей из композиционных материалов. Наиболее широко
распространены композиционные материалы на полимерной основе, армированные стеклян-
ными, углеродными, борными и органическими волокнами и тканями [1–4]. Эти материалы,
как правило, состоят из двух или более компонентов, обладающих различными физико-
химическими свойствами и объединенных в единую макроструктуру. Композиты имеют вы-
сокую прочность в сочетании с низкой плотностью, способны сопротивляться коррозии и
химическому воздействию, а также обладают сравнительно невысокой стоимостью. Однако
полимерные композиты имеют ряд недостатков. Как известно, для изготовления деталей из
полимерных композиционных материалов применяются экструзия, прессование, намотка и
другие технологии, позволяющие получать необходимый профиль детали, однако во многих
случаях для получения готовой детали необходимо применять механическую обработку. При
этом возникают трудности, связанные со спецификой свойств полимерных композитов: де-
струкция полимерного связующего и появление в процессе механической обработки твердых
структур, оказывающих негативное влияние на состояние режущей кромки инструмента; вы-
сокая твердость наполнителя; слоистая структура и т.п.[3]. Это вызывает интенсивный износ
режущего инструмента и приводит к неудовлетворительному качеству обработанной по-
верхности.
Эти проблемы решаются подбором инструментальных материалов и режимов обра-
ботки, обеспечивающих высокую износостойкость режущего инструмента и качество обра-
ботанной поверхности. Также важен выбор оптимальной конструкции режущего инструмен-
та для производственных условий, который может обеспечиваться путем применения про-
граммного обеспечения, позволяющего автоматизировать процесс разработки технологиче-
ского процесса [5–13].
Высокая износостойкость режущего инструмента может быть достигнута применени-
ем твердых сплавов, однако они трудно поддаются обработке при формировании режущей
кромки инструмента [14–17]. Проблема решается путем использования технологий электро-
алмазной обработки с одновременной правкой круга и травлением детали, которые позволя-
ют получать поверхности твердых сплавов высокого качества с максимальной производи-
тельностью [18, 19].
Среди широкой номенклатуры полимерных материалов стоит выделить композиты,
армированные стеклянными тканями. Они применяются для изготовления деталей различно-
го назначения, например, в машиностроении в качестве конструкций, работающих в услови-
ях повышенных вибраций и знакопеременных нагрузок, сеток для армирования отрезных
дисков или фильтров очистки отходящих газов от пыли и промышленных стоков, в автомо-
билестроении в качестве глушителей, панелей, теплоизоляционных прокладок и т.п., в судо-
строении в качестве теплозвукоизоляции судовых установок и оборудования, в авиационной
промышленности и ракетостроении в качестве корпусных деталей самолетов и ракет, в хи-
мической промышленности в качестве химически стойких труб и емкостей для хранения аг-
рессивных жидкостей, в металлургии в качестве фильтров для расплавов металлов при литье
и т.п. [3, 4].
Теория.
Исследования по разработке рациональных параметров резания стеклопла-
стиков и стеклотекстолитов отражено в работах [20–32], в которых приведены результаты
исследований качества обработанной поверхности, мощности обработки и стойкости режу-
щего инструмента в зависимости от режимов резания. При этом варьирование скорости ре-
зания не осуществляется, а устанавливается ее максимальное значение, ограниченное воз-
можностями технологического оборудования,что связано с особенностями протекания пла-