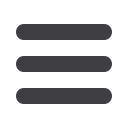
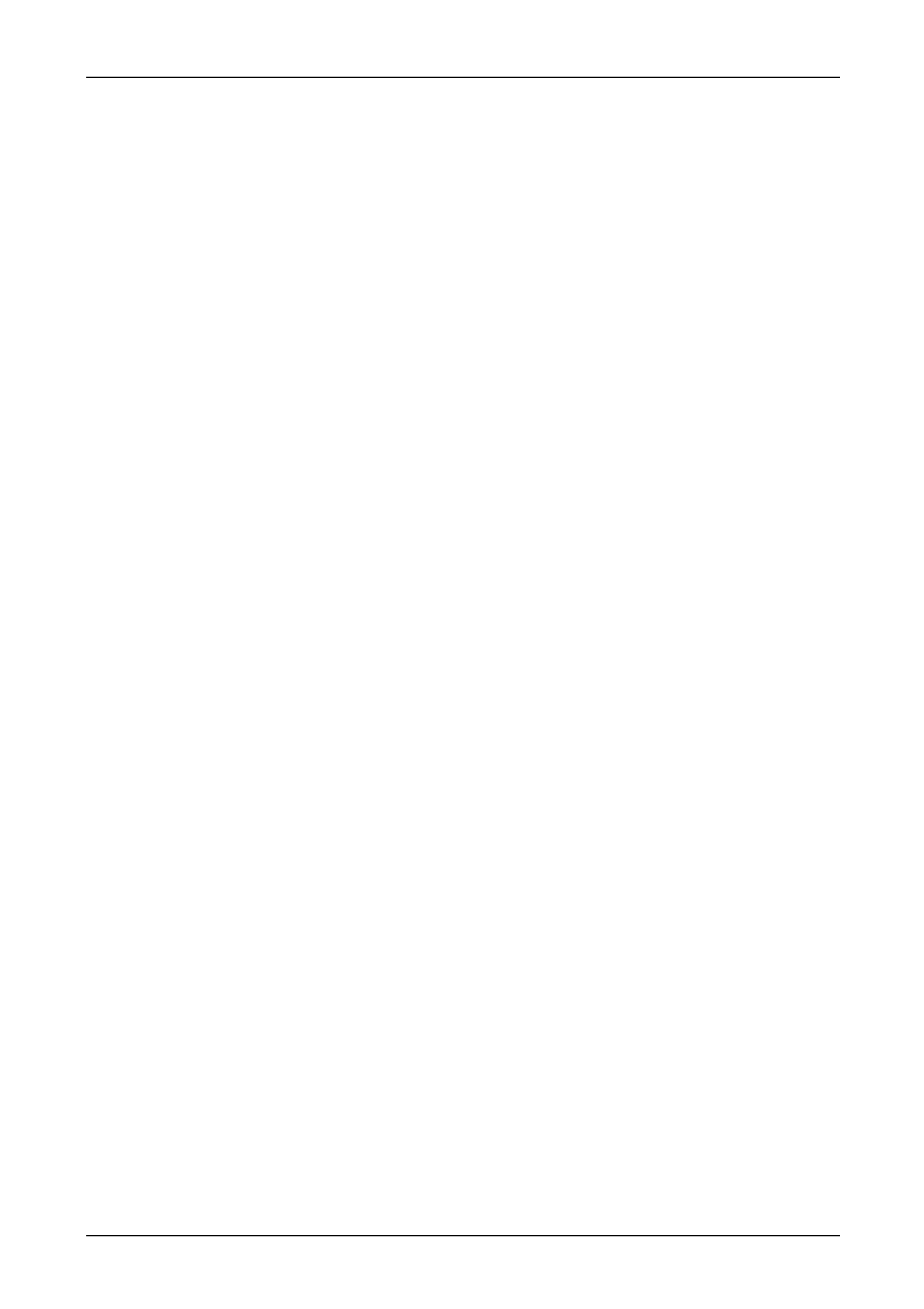
Механики XXI веку. №16 2017 г.
182
УДК 621.9
Организация структуры комлекса проектных процедур для
автоматизации технологической подготовки
механообрабатывающего производства высокоточных изделий с
учетом требований сборки
Назарьев А.В.
a
, Бочкарёв П.Ю.
b
ФГБОУ ВО «Саратовский государственный технический университет имени Ю.А. Гагарина», 410054,
Саратов, ул. Политехническая, 77.
a
alex121989@mail.ru,
b
bpy@sstu.ruКлючевые слова:
сборочное производство; комплекс проектных процедур технологической
подготовки производства; высокоточные изделия; граф размеров, граф сопряжений элементов сбо-
рочной единицы; граф технологического процесса
Проблема совершенствования машиностроительных производств приобретает первосте-
пенное значение. Требуемая точность высокоточных изделий достигается при традиционных ме-
тодах изготовления усложнением технологического оборудования и использованием информацион-
ных и измерительных технологий. В настоящее время функциональная точность высокоточных из-
делий превзошла точность обрабатывающего и сборочного оборудований почти на порядок. Это
привело к возникновению проблемы достижения заданного качества и точности высокоточных из-
делий при их изготовлении. На сегодняшний день наблюдаются разрозненные решения отдельных
задач этой проблемы, отсутствует наиболее приближенная к реальным требованиям концепция
системы в целом. В данной статье формируется структура комплекса проектных процедур, кото-
рый основывается на установлении связи между технологической подготовкой механообрабаты-
вающего и сборочного производств. Также в статье рассматриваются математическая модель
представления и анализа деталей и сборок (исходными данными являются полученные графы со-
пряжений сборочной единицы и графы размеров) и подход для автоматизации расчета технологиче-
ских размерных цепей (исходными данными являются граф технологического процесса и размерные
цепи).
Перед современным производством стоит задача выпуска в короткий срок небольши-
ми партиями изделий высокой функциональной точности. Унификация и организация груп-
пового производства позволяют обеспечить выпуск небольших партий изделий в заданные
сроки, а требуемая точность достигается при традиционных методах изготовления усложне-
нием технологического оборудования и использованием информационных и измерительных
технологий. Но как только требуемая функциональная точность изделий (приборов и машин)
превзошла точность обрабатывающего и сборочного оборудования почти на порядок, воз-
никла проблема достижения заданного качества и точности изготовления высокоточных из-
делий при их изготовлении [1]. Решение данной проблемы достигается в большинстве случа-
ев затратными способами в виде многочисленных переборок, доработок и уточнения конст-
рукции, поскольку эти требования в серийном производстве находятся на грани максимально
технологически достижимых. Кроме того, значительные трудности, особенно на этапе сбо-
рочного производства, вызывает влияние непознанных и неуправляемых причин, вызываю-
щее непрогнозируемый разброс заданных эксплуатационных характеристик [2, 3, 4]. На рис.
1 представлены методы достижения точности при сборке изделий (методы достижения точ-
ности замыкающего звена).
Представленные методы достижения точности сборки не являются универсальными и
зависят от типа производства и конструктивных особенностей изготавливаемых изделий.
Например, метод селективной сборки обеспечивает требуемое качество изделий из деталей,
точность изготовления которых значительно меньше требуемой функциональной; он обеспе-
чивает низкую себестоимость изготовления изделия, но эффективен только в массовом про-
изводстве. Кроме того, при сборке высокоточных изделий, в основном, не предусматривает-