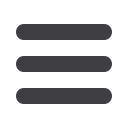

Эксплуатация и ремонт машин и оборудования
351
Введение.
Основные объемы минеральных ресурсов во всем мире добываются откры-
тым способом, при этом удельный вес открытой добычи по многим полезным ископаемым
продолжает возрастать. При этом крупных глубина карьеров увеличивается. В связи с посте-
пенным ухудшением горно-геологических условий отработки месторождений к карьерному
оборудованию предъявляются все более высокие требования [1]. Для обеспечения селектив-
ной выемки полезных ископаемых, повышения устойчивости бортов карьеров, ужесточения
требований безопасности ряд предприятий отказываются от буровзрывной подготовки пород
к выемке и переходят на механическое рыхление. В последние десятилетия ведется интен-
сивное совершенствование горных машин и оборудования, создаются новые образцы. Боль-
шое развитие получила техника для безвзрывной выемки прочных горных пород. Карьерные
комбайны и фрезерные машины, оборудованные фрезерным рабочим органом, разрабатыва-
ют не только плотные и полускальные, но и отдельные скальные породы [2–5], с обеспече-
нием высокой селекции пород. При этом, единичная мощность горного оборудования, задей-
ствованного на открытых горных работах продолжает увеличиваться [6]. Во многих случаях
механическое рыхление оказывается экономически более выгодным, чем рыхление взрывом.
Постановка проблемы.
При открытой разработке месторождений значительное ко-
личество минеральных запасов остается за техническими границами карьеров и в целиках
различного назначения, отработка которых традиционными способами и экономически не
целесообразна или технически невозможна, доработка данных относительно небольших за-
пасов подземным способом также нецелесообразна. Отдельным рядом стоят маломасштаб-
ные месторождения, которые зачастую обладают высоколиквидными запасами минерально-
го сырья в крутопадающих рудных телах расположенных на небольшой глубине, однако раз-
работка таких месторождений по традиционным технологиям также зачастую оказывается
нерентабельной. Поэтому важной технической задачей в настоящее время является создание
горного оборудования позволяющего с минимальными затратами разрабатывать с поверхно-
сти маломасштабные крутопадающие месторождения и дорабатывать рудные тела (включая
крутопадающие) средних и крупных карьеров.
Результаты исследований.
В настоящее время созданы технологические решения,
позволяющие дорабатывать горизонтальные и наклонные пласты полезных ископаемых [7-
8]. Так в угольной промышленности США в 1950-х годах появилась так называемая «при-
бортовая отработка угля», позволяющая разрабатывать залегающие на небольшую глубину и
находящиеся за предельными контурами карьера пласты без выполнения дополнительных
вскрышных работ. Для отработки таких пластов применялись шнекобуровые агрегаты, ос-
нащённые горизонтальными шнеками большого диаметра. У откоса уступа с обнажённым
выходом угольно пласта устанавливалась шнекобуровая машина так, чтобы ось шнека сов-
падала с линией падения (восстания) пласта. За счёт углубления вращающегося бурового
става в забой, шнек выдавал разрушенный уголь из скважины в приёмный бункер машины,
откуда по конвейеру тот попадал в транспортное средство, либо штабель на площадке усту-
па. Между соседними скважинами оставлялись целики шириной 0,3…0,6м. Если на началь-
ном этапе развития данной технологии глубина бурения не превышала 60м, то через 30-
40лет глубина бурения достигала 200м и более. В настоящее время по данной технологии
отрабатываются пласты угля мощностью от 0,4 до 3м, залегающие под углом падения 0-30
.
Применяются одно-, двух- и трёх шпиндельные агрегаты, способные бурить одновременно
одну, две и три скважины соответственно.
В конце 1970-х годов началось создание комплексов прибортовой добычи угля нового
технологического уровня, развивающие технологии шнекобуровой выемки, с использовани-
ем подземных проходческих комбайнов. Первые опытные образцы The Тhin Seam Miner
(разработчика тонких пластов) были выпущены компанией Dieseko (Голландия). На основ-
ной раме машины установлены: механизм балки-толкателя с двумя мощными гидроцилинд-
рами для подачи режущего модуля на угольный забой и извлечения его в исходное положе-
ние, вращатель шнекового конвейера и загрузочный стол шнекового конвейера. Шнековый
конвейер состоит из коробчатых секций длиной по 6,1м. Внутри короба каждой секции раз-