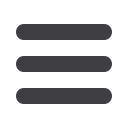
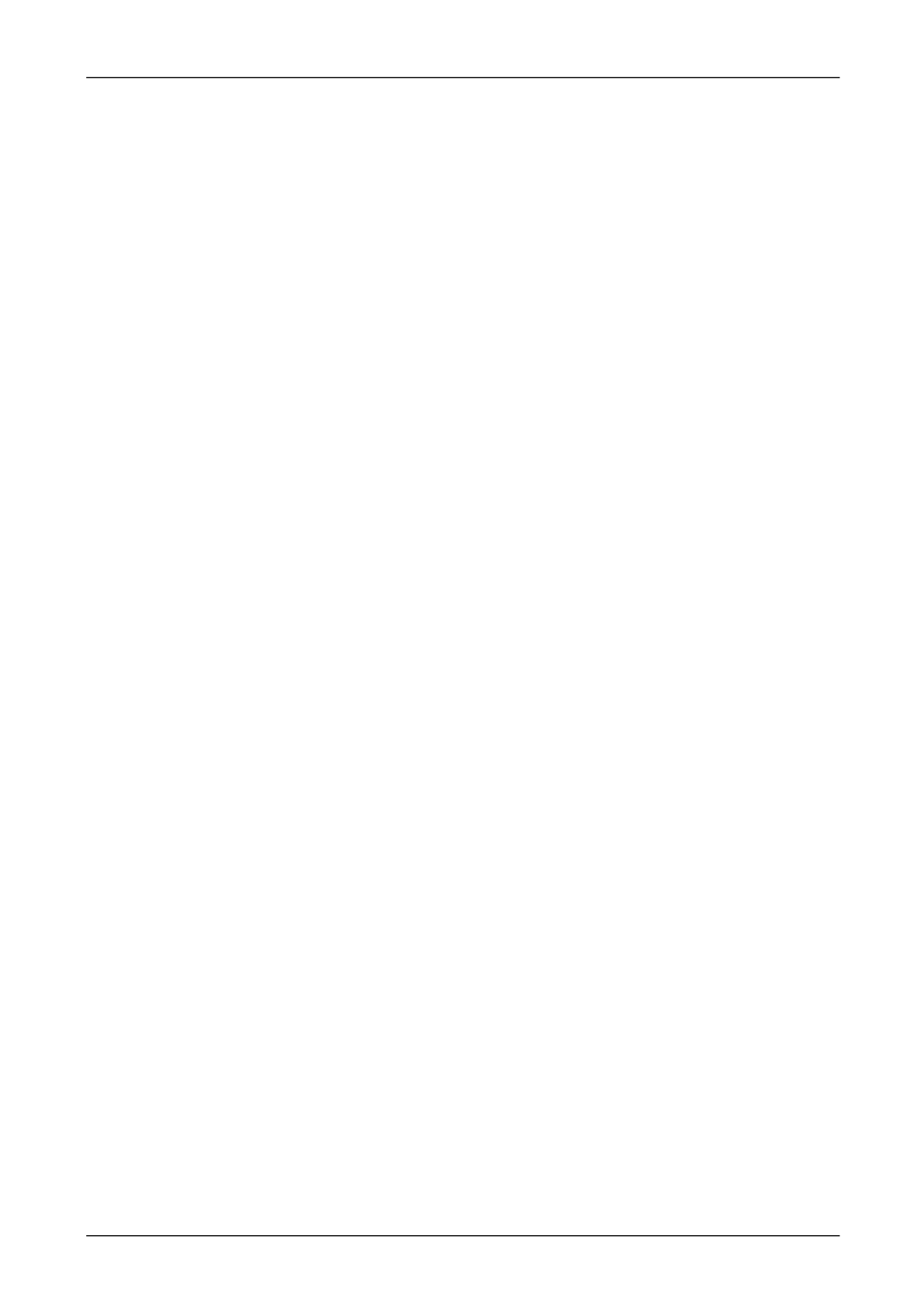
Механики XXI веку. №16 2017 г.
166
блема рационального выбора эксплуатационных нагрузок при расчете подобных деталей на
усталостную прочность является основополагающей для повышения надежности привода.
Общепринятый подход к решению обозначенной проблемы базируется на использо-
вании в конструкторских расчетах функциональных зависимостей распределения времени
функционирования привода при различных сочетаниях частот вращения и действующих
крутящих моментов, данные о которых получают на базе информации об условиях эксплуа-
тации станков-аналогов. Однако особенность расчетов комплектующих привода станков на
первоначальном этапе проектирования заключается в использовании и учете эквивалентных
нагрузок, а не эквивалентных напряжений, поскольку определенное конструктивное испол-
нение узлов и их деталей, как правило, еще не известно.
При создании же принципиально новой конструкции интегрального станка, когда
аналоги либо отсутствуют, либо только в первом приближении соответствуют вновь разра-
батываемому оборудованию, задача существенно усложняется. Связать это можно только с
тем, что эксплуатационные нагрузки многоцелевого металлообрабатывающего оборудования
представляют собой систему коррелированных случайных величин, зависящих от многочис-
ленных и разнообразных факторов, сочетания которых многовариантны и носят вероятност-
ный характер [31]. Более того, требуется определенный прогноз условий эксплуатации про-
ектируемого станка задолго до их проверки на практике. Поскольку, на стадии разработки
технического предложения достоверная информация чаще всего отсутствует, а вопрос обос-
нованного назначения рациональных (оптимальных) эксплуатационных нагрузок на данный
момент не решен, то основным инструментом при поиске данных факторов является исполь-
зование стандартных методик и рекомендаций, как показывает практика, приводящих к за-
вышенной металлоемкости технологического оборудования.
Цель работы
: разработка методики математического моделирования распределения
эксплуатационных характеристик.
Теория.
Эффективная мощность (
Р
[кВт]), частота вращения (
n
[мин
-1
]) и крутящий
момент (Т [Н м]) на шпинделе – это те главные эксплуатационные характеристики техноло-
гического оборудования, которые образуют систему взаимосвязанных случайных величин,
зависящих от большого числа аддитивно и мультипликативно действующих факторов (пара-
метров технологических операций). Исходя из этого, в основу математической модели, адек-
ватно отражающей специфику условий функционирования гибридного металлообрабаты-
вающего оборудования [32, 33], целесообразно положить принцип суперпозиции. В соответ-
ствии с ним дифференциальная функция распределения для системы эксплуатационных ха-
рактеристик имеет вид:
1
,
,
q
q q
yx fp
yxf
, (1)
где
yx f
q
,
- дифференциальная функция элементарных (частных) распределений экс-
плуатационных характеристик
х
и
у
(соответственно
T
и
n
) для некоторых (
q - x
) условий об-
работки (мощность
Р
в число аргументов этой функции не входит, так как является произ-
водной от
n
и
T
);
p
q
- вероятность работы интегрального станочного комплекса в этих усло-
виях;
- число разных условий обработки, реализуемых на станке.
Статистическими исследованиями установлено, что при определенных сочетаниях
технологических факторов для некоторых условий обработки, рассматриваемые эксплуата-
ционные характеристики можно описать логарифмически нормальным законом распределе-
ния. В связи с этим произведем в формуле (1) замену переменных:
T x
ln
;
n y
ln
, после че-
го функцию
f(x, y)
можно представить в виде поверхности распределения (рис. 1). Всю на-
чальную информацию, необходимую для ее создания, можно получить на этапе прогнозиро-
вания технических характеристик технологического оборудования [31–33] или взять из тех-
нического задания на его проектирование.
В свою очередь, для исследования нагрузок, которые будут действовать на отдельные
элементы привода, вместо поверхности более целесообразно использовать картину распре-